Daily Progress Report (DPR) in construction
The results of the planning and design process of a project are the Daily Progress Reports (DPRs). With the help of Livefield app, it is easy to make a DPR report.
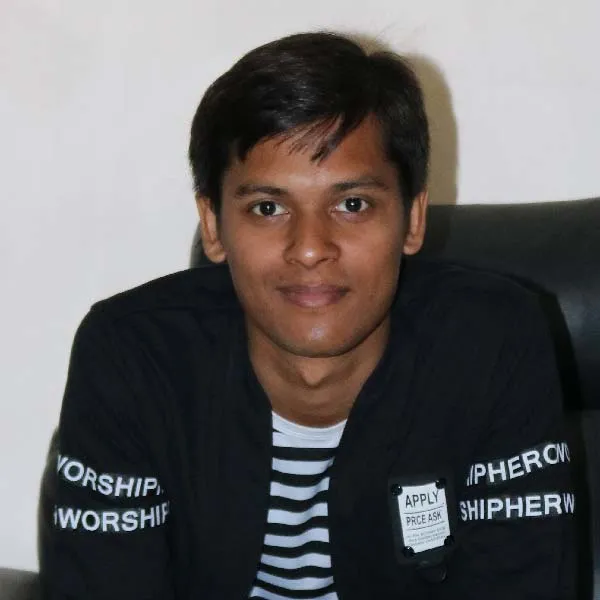
The word “Lean Construction” has been commonly heard about a lot recently when discussing to construction efficiency, but what precisely is lean construction? Planning, organizing, and communicating effectively are at the heart of lean techniques, which aim to minimize wastage and boost productivity. Maybe the Leaning Tower of Pisa wouldn't be leaning if it had been constructed utilizing lean construction methods!
Lean concepts were really first developed by Toyota for producing car components in the mid-20th century, but have since spread to other sectors, including construction. Worksite efficiency and sustainability may be improved using the same technique that has transformed factories, although certain adjustments may be necessary owing to the highly uncertain nature of construction projects. The right mix of lean construction techniques and cutting-edge construction technology can make project management easier and more effective than ever before.
With appropriate execution and the correct tools, lean construction may help projects move along easily, and for subcontractors, this can be a big advantage. From the outset, lean construction facilitates communication among subcontractors, general contractors, and project owners. This implies that fewer conflicts erupt, and there are consequently fewer delays caused by misunderstanding. In this way, projects are completed faster, increasing the likelihood of customer loyalty and repeat business.
Using lean construction methods doubles the chance of completing a project on time and under budget, according to the Lean Construction Institute. Increased safety and quality of construction are achieved, while waste is reduced. To demonstrate the advantages of lean construction, we came across the following infographic, prepared by McCarthy Building Companies, Inc.
The purpose of lean construction approach is to optimise efficiency by minimising needless and unexpected expenditures. It is based on five fundamental principles: defining value, identifying value streams, establishing flow, pull planning, and continuously improving. These strategies are used throughout the various phases of a project, and include all project personnel.
While it is essential to know what the client needs, it is as important to know why they wish to have it constructed. The best method to find out what the client thinks is to just ask them. As long as you have a clear understanding of your client's needs, you can avoid wasting time speculating about what they want from the construction. When you begin a project by establishing open communication with your client, you show them that you aren't merely doing the task, but that you genuinely care about producing a great, satisfied and quality result.
After determining what your client values, you can organize your project around that value and ensure that you will meet the customer's expectations at the completion of the project. M Data from the project's participants is collected and analyzed to develop a visual plan that maximizes the use of both resources and time while mapping a value stream. Make sure you include any potential waste elements in your project's value stream when mapping it out. When you think about problems before they happen, you can figure out how to avoid them and keep your project on track, so you don't have to deal with them.
It is much easier to maintain a steady stream of development throughout the course of a project if you have mapped your value stream. Communication between subcontractors is an essential part of a project's flow. Projects are completed more quickly and with fewer problems when subcontractors collaborate to keep things running smoothly. When a flow is established, procedures are optimised to execute as rapidly as possible.
Lean construction's most essential part is pull planning. In a pull planning meeting, everyone engaged in a project, including subcontractors, gathers together. Sticky notes are used by these people to keep track of significant project milestones and stages, moving backward from the desired finish date. If you're utilising pull planning, you may get a better sense of when particular milestones will be achieved and when they'll be completed.
Lean construction approaches, in its final element, embrace the idea that there is always space for improvement. A post-project review may help you find areas for improvement for future projects, even if everything went according to plan throughout the course of the work. If lean construction methods are followed throughout a project, it is hoped that the project will be finished on time and under budget. However, delays or minor elements are occasionally overlooked in planning, resulting in setbacks. You can keep improving your performance if you recognise that there is always room for improvement.
If the goal is to optimise efficiency using lean construction principles, it makes logical to use technologies that may help in the process. Construction management software help to improve communication between subcontractors and general contractors, as well as from the field to the office. Lean construction processes are enhanced by software like Livefield that can measure production, capture images and videos on site, and record any delays or issues. This combination helps businesses in completing projects on schedule and under budget. Lean construction approaches, which are increasingly being used by major participants in the construction industry, will lead to increased productivity, fewer conflicts, and better-quality products. Additionally, you may ensure that none of your structures will ever bear the label "The Leaning", since you can prevent it from ever appearing in their name.
Integrate lean management approach in you project using Livefield to minimize wastages and boost productivity. Sign up now.
We can help you to manage your project for better business revenue.
Experience seamless project management with our free plan!