Daily Progress Report (DPR) in construction
The results of the planning and design process of a project are the Daily Progress Reports (DPRs). With the help of Livefield app, it is easy to make a DPR report.
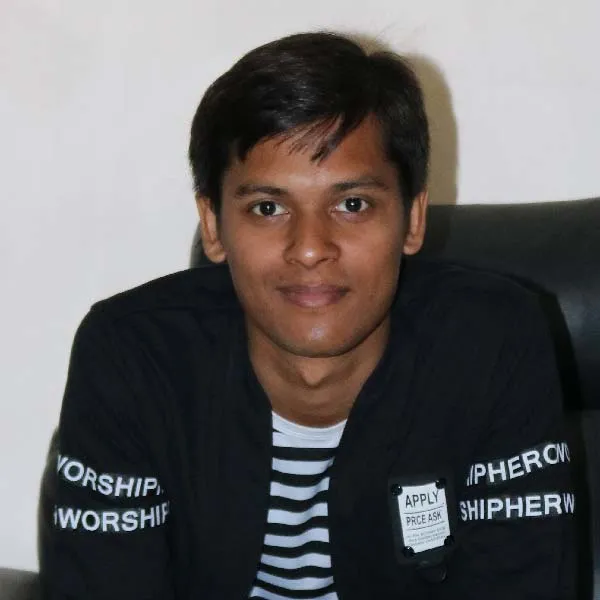
The most significant role of a design professional has traditionally been to design a building or structure such that it conforms to accepted engineering practices, local building codes, and is safe for the public. The safety of construction workers is generally considered to be in the hands of contractors. However, design professionals can improve construction safety by making safer choices in the design and planning stages of a project. It would result in fewer on-site decisions by the contractor that may create hazards for the work force.
Within Europe, construction designers are legally bound to design out risks during design development to reduce hazards in the construction and end use phases via the Mobile Worksite Directive (also known as CDM regulations in the UK). In US also, the National Institute for Occupational Safety and Health (NIOSH) in the United States is a major contributor and promoter of PtD policy and guidelines.
Prevention through Design anticipates and minimizes occupational safety and health hazards and risks at the design phase of structure considering workers through the entire life cycle, from the construction workers to the users, the maintenance staff, and, finally, the demolition team. PtD is the optimal method of preventing occupational illnesses, injuries, and fatalities by designing out the hazards and risks. A strategic goal of the Prevention through Design (PtD) is for designers, engineers, machinery and equipment manufacturers, health and safety (H&S) professionals, business leaders, and workers to understand the PtD concept.
What are the benefits of Prevention through Design (PtD)?
In order to improve the design process, suggestions can be taken from targeted resources such as safety design manuals and checklists, ideas generated by the researchers, and interviews with industry personnel. Manuals and checklists typically address hazards during the startup, operation, and maintenance stages of a project. The on-site workforce and others who visit the job site generally provide the most design suggestions. They are involved in the day-to-day construction activities and are frequently exposed to job site hazards. Any effort that designers put to addressing construction worker safety is voluntary, since law does not place any great responsibility for safety on them.
The following list documents possible design suggestions with their purposes.
Sr. | Suggestion | Purpose |
---|---|---|
1 | The design of prefabrication systems should be based on units that can be built on the ground and erected in the required place. | It would reduce the worker’s exposure to falls and being struck by any falling objects. |
2 | Design underground utilities such that they can be placed using trenchless technologies. | This would ensure the elimination of the safety hazards associated with trenching. |
3 | There should be adequate clearance allowed between structures and power lines. | Overhead power lines are hazardous when operating cranes. |
4 | Permanent anchorage points should be designed in the residential roofs. | Provide fall protection anchorage for roofing contractors during future maintenance. |
5 | Cable type lifeline system are required to be designed for tower structures. | These will allow workers to hook onto the structure and move up and down during any future maintenance. |
6 | The window sills should be designed 42 inches above the floor. | This will eliminate need for fall protection during construction and future maintenance. |
7 | Design permanent guardrails around skylights. | Prevent workers from falling through skylights. |
8 | Design components to facilitate prefabrication in the shop or on the ground so that they may be erected in place as complete assemblies. | Reduce worker exposure to falls from elevation and the risk of workers being struck by falling objects. |
9 | Design steel columns with holes in the web at 0.53 and 1.07 m above the floor level to provide support locations for guardrails and lifelines. | By eliminating the need to connect special guardrail or lifeline connections, such fabrication details will facilitate worker safety immediately upon erection of the columns. |
10 | Design beam-to-column double connections to have continual support for the beams during the connection process by adding a beam seat, extra bolt hole, or other redundant connection point. | Continual support for beams during erection will eliminate falls due to unexpected vibrations, misalignment, and unexpected construction loads. |
11 | Minimize the number of offsets in a building plan, and make the offsets a consistent size and as large as possible. | Prevent fall hazards by simplifying the work area for construction workers. |
12 | Design underground utilities to be placed using trenchless technologies. | Eliminate the safety hazards associated with trenching, especially around roads and pedestrian traffic surfaces. |
13 | Design roadway edges and shoulders to support the weight of construction equipment. | Prevent heavy construction equipment from crushing the edge of the roadway and overturning. |
14 | Position mechanical, piping, and electrical controls away from passageways and work areas, but still within reach for easy operation. | Controls that protrude into passageways and work areas, or are hard to operate, hidden, or inaccessible, create safety hazards for construction and maintenance workers. |
15 | Allow adequate clearance between the structure and overhead power lines. Bury, disconnect, or reroute existing power lines around the project before construction begins. | Overhead power lines that are in service during construction are hazardous when operating cranes and other tall equipment. |
16 | Route piping lines that carry liquids below electrical cable trays. | Prevent the chance of electrical shock due to leaking pipes. |
17 | Do not allow schedules with sustained overtime. | Workers will not be alert if overtime is maintained over a sustained period. |
A project's primary focus should always be on ensuring worker safety. A digital checklist application is the suggested best practise to improve worker safety. When it comes to making the transfer from paper checklists, consider Livefield - Construction Management Software that has all of the aforementioned advantages and much more.
Furthermore, Livefield is more than a checklist app; it's a construction management software that lets you oversee every aspect of your construction project and achieve first time quality. Sign up now to get Started free.
We can help you to manage your project for better business revenue.
Experience seamless project management with our free plan!