Daily Progress Report (DPR) in construction
The results of the planning and design process of a project are the Daily Progress Reports (DPRs). With the help of Livefield app, it is easy to make a DPR report.
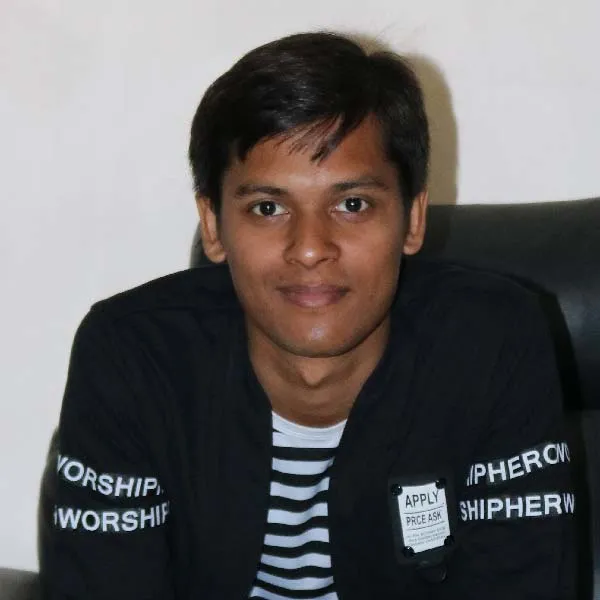
MIVAN is an aluminum formwork system that was developed by a construction company based in Europe. The manufacturing of these formwork systems was initiated by the Mivan Company Ltd. from Malaysia in 1990. Today, Mivan Co. Ltd. is responsible for supplying over 30,000 sqm of aluminium framework that is utilized globally. The technology has been widely utilized in Europe, Gulf Countries, Asia, and various other regions across the globe. It is a cost-effective alternative to the labor-intensive and time-consuming traditional construction methods. Mivan technology construction proves to be cost-effective, particularly for large-scale construction projects. It completely eliminates the use of bricks, opting instead to construct all components such as beams, walls, slabs, staircases, etc., using concrete. Modular kitchens have become a popular choice over traditional ones due to their enhanced space efficiency, aesthetic appeal, and time-saving benefits. Similarly, the implementation of mivan technology formwork has greatly benefited the real estate sector by facilitating easy assembly and faster construction processes.
The primary component of the MIVAN formwork is the panel. This panel consists of an extruded aluminum rail section that is welded to an aluminum sheet. This manufacturing process creates a panel that is lightweight yet has a high stiffness to weight ratio. As a result, the panel experiences minimal deflection when subjected to the weight of concrete. They can be manufactured in any size and shape to meet the specific requirements of different projects.
The pre-cast technology is an extension of the structural load-bearing walls and flat slab system. In this method, different modules of the structure are cast in factories away from the site and then brought together for assembly on-site. The main difference between MIVAN technology and pre-cast construction is that MIVAN uses a monolithic construction approach, while pre-cast involves joining pre-cast elements together.
In this construction method, cast-in-situ concrete walls and floor slabs are used to create a structural system that is poured in one continuous process. To expedite the construction process, early removal of forms can be accomplished through the use of hot air curing or curing compounds. At the construction site, we erect large forms that are the size of rooms for the walls and floor slabs. These forms are both strong and sturdy, and they are fabricated with precision for easy handling. The concrete is carefully produced in RMC batching plants, ensuring strict quality control measures are in place. It is then transported to the construction site using transit mixers.
Mivan shuttering is widely used for construction purposes across the globe, including in Asia, Europe, and the Middle East. Mivan Shuttering is widely utilized in India for the ambitious project initiated by the Indian government, known as "Housing for All by 2024".
While Mivan formwork does offer numerous advantages, it is important to acknowledge its limitations as well. However, the limitations do not present any significant issues.
While Mivan formwork does offer numerous advantages, it is important to acknowledge its limitations as well. However, the limitations do not present any significant issues.
Component type | Component | Purpose |
---|---|---|
Wall Componnet | Wall panel | An important component of Mivan outlines the structure of the wall made out of an aluminum sheet precisely cut to fit the accurate size of the wall. |
Rocker | This sheet is L-shaped and has holes specifically designed for stub pins to securely hold the wall panels in place. | |
Kickers | The purpose of this is to serve as a ridge that securely holds the wall panel in place. It accomplishes this by outlining the top of the panel along the wall face. | |
Stub pin | An important component, that fixes every wall component from each other. | |
Beam side panel | The edges of the beams are shaped by cutting a rectangular structure into the required size. | |
Prop head and panel for soffit beam | In general, beams are typically suspended without support from the bottom. However, prop heads are utilized to provide the necessary support from below. The formwork features a V-shaped top, making it easy to remove without any trouble. | |
Deck component | Deck panels | A flat surface upon which the slab is cast. |
Deck prop and prop length | Deck prop works the same as deck prop, here it is used to hold the slab and take the weight coming from the deck panel. On the other hand, prop lengths provide vertical support to the deck prop, which you can adjust according to the height of the slab | |
Soffit length | This component offers support to the deck panels located at the edge of the room. | |
Other Component | External corner | |
Internal corner | ||
Internal soffit corner | ||
External soffit corner |
Wall reinforcing steel is utilized to provide structural support to buildings and assist in holding the concrete in place until it reaches approximately half of its required strength. The aluminum formworks are cast around the factory-made steel mesh and then directly erected on the construction site.
Prefabricated room-sized walls and floor slabs are erected along the wall, reinforcing steel. The aluminium alloy slabs are precisely manufactured and have a user-friendly design, making them easy to handle. These structures also integrate spaces for windows, ducts, doors, and other features like staircases, façade panels, and chajjas. The forms are joined together using the pin and wedge system, allowing for quick dismantling once the concrete structure is complete.
Once the forms have been cast, high-quality concrete is poured. The concrete is molded into the shape of the cast, which is then removed to create space for a structure constructed entirely of cement concrete, reinforced by wall reinforcing steel. The aluminum forms have the ability to be reused for a minimum of 250 times, which significantly reduces waste generated from the construction site.
The resulting structure is precise, seamless, and polished. It has a high tolerance and does not require any additional plastering. Consequently, it helps to save time, effort, and money.
Sr. No. | Parameter | Mivan shuttering system | Regular formwork |
---|---|---|---|
1. | Speed of development | 7 days/floor | Minimum 21 days/floor |
2. | Quality of surface finish | Excellent | Putting is required |
3. | Pre-planning of formwork system | Required | Not required |
4. | Type of construction | Cast-in-situ cellular construction | Simple RCC |
5. | Wastage | Very little | Comparatively higher |
6. | Accuracy in construction | Accurate | Accuracy lesser than modern systems |
7. | Coordination between offices | Essential | Not required |
8. | Seismic resistance | Good resistance | Comparatively lesser |
9. | Dismantling floor piece frames without expelling props | Possible | Impossible |
We can help you to manage your project for better business revenue.
Experience seamless project management with our free plan!