Daily Progress Report (DPR) in construction
The results of the planning and design process of a project are the Daily Progress Reports (DPRs). With the help of Livefield app, it is easy to make a DPR report.
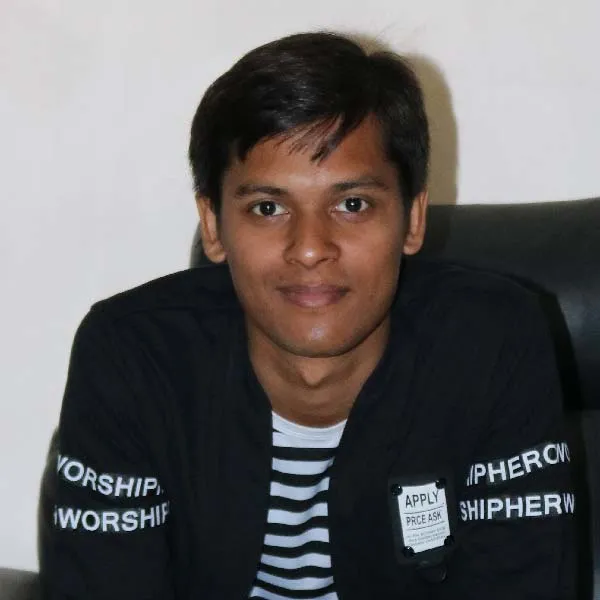
Hey guys, In engineering companies, when we spot a Non-Conformance, we create a Non-Conformance Report! They happen when a product, service or procedure doesn'tpos;tpos;tpos;t meet the quality regulations or requirements set by the standards. They may be present in any department within your organization, activities, operations, processes, and production. A Non-Conformance Tracking System is frequently utilized to effectively manage Non-Conformances. This article explores the role of Non-Conformance Reports in enhancing quality management.
A Non-Conformance Report (NCR), also referred to as a Non-Conformity Report, is a formal document that highlights any inconsistencies between the actual state of a product, service, or process and the quality standards" specified requirements. Non-Conformance Reports can be generated for any area within an organization, but they are most commonly associated with construction issues and operations.
The Non-Conformance Report (NCR) is a meticulously structured document that details the specific non-conformity found. It helps to comprehend the underlying threat posed by violating the requirements and enables individuals to take appropriate subsequent actions. In addition, Non-Conformance Reports (NCRs) aid in developing a regulatory plan of action to prevent similar incidents from occurring in the future and facilitate compliance and audits.
Creating a Non-Conformance Report (NCR) allows for a thorough analysis and audit of any issues, ensuring that they are fixed correctly and in compliance with safety and quality standards.
A Non-Conformance Report is a structured document that records the details of a Non-Conformance that has been identified. Organizations, projects, or individuals who fail to meet quality and safety standards may be held accountable for non-compliance with the requirements.
Non-Conformance Reports are usually tailored and standardized to suit an organization's specific needs. Put simply, an organization will opt to generate a Non-Conformance Report (or multiple reports) that meets their specific requirements. Here, we present two templates for Non-Conformance Reports - one for simple cases and the other for more complex situations.
Smaller organizations may opt for a concise non-conformance report that only includes basic information and does not provide details on actions and responsibilities.
Organizations that are larger in size and those that prioritize compliance will generally require a more comprehensive report.
Organizations have the ability to tailor Non-Conformance Reports to meet their unique organizational requirements. One way to enhance the Report is by incorporating checkboxes and text fields to gather comprehensive data about every Non-Conformance.
A Non-Conformance Report may include the following types of data:
Utilizing a structured template for each department is beneficial in maintaining the quality control system as it ensures that no information is overlooked.
Typically, the severity and impact of a Non-Conformance determine whether it is classified as Minor or Major.
A Non-Conformance Report that is classified as minor is considered to be less severe and has a lower impact on the operation. Minor non-conformances typically have straightforward corrective actions that do not necessitate substantial modifications to the operation or process. Minor non-conformances refer to small events or slip-ups that are easily correctable.
Some examples of these are:
Addressing a minor non-conformance is typically a simple process since the necessary corrective action is not extensive. If a machine that is not on the approved list is used, the corrective action could be as simple as updating the list of approved machines or using a different machine in the future.
Major Non-Conformances refer to violations that have a significant impact on the quality of structure or operation, and therefore require communication up the management chain. There are numerous and significant violations of requirements.
Some examples of these are:
In this case, the corrective action may be complex and extensive, and it might necessitate substantial modifications to the scheduling or operations. Major Non-Conformances are expected to have an impact on the entire project. It is essential to inform all parties involved, including teams and organizations, in a timely manner.
Non-Conformance control is crucial for enhancing quality and project goal as it helps to determine whether you are meeting the client's requirements or your own standards. Non-Conformance Reports are useful tools for identifying and addressing issues. Completing a Non-Conformance Report enables you to take appropriate measures to prevent repeating the same error in the future.
Customers complain when they receive quality that fails to meet their expectations. Non-Conformance Reports assist businesses in identifying potential customer complaints and preventing them from occurring.
Businesses can avoid the expenses associated with rework, scrap, and waste by detecting and addressing issues early on. Implementing Non-Conformance Reporting can assist companies in preventing the expenses associated with quality, safety, rework issue.
In addition, opting not to fix or maintain technical requirements based on the Non-Conformance decision can result in cost savings for your operations. Maintaining transparency and open communication is crucial to keep all stakeholders informed and knowledgeable about the current situation.
Businesses can enhance the efficiency of their operations by proactively addressing problems at an early stage. Non-Conformance Reports can assist companies in identifying and eliminating bottlenecks, as well as streamlining processes.
You can effectively communicate, monitor, and oversee the progress of every Non-Conformance from identification to resolution. Ensuring that corrective and preventative actions are carried out in a timely manner and that the root cause of the problem is identified and addressed will be helpful.
Non-conformity reports are useful in identifying the underlying causes of non-conformities and implementing measures to prevent their recurrence. Improving the quality of products and services and enhancing the efficiency of operations can be achieved through this.
Having a clear understanding of what went wrong and why is crucial for someone who needs to write a report on an issue that has arisen. This knowledge can help prevent the same mistake from happening again. Implementing a Non-Conformance reporting system can aid in learning from mistakes and enhancing the quality of construction.
Numerous businesses are obligated to adhere to regulatory requirements such as ISO, ECSS, AS9100, etc. which necessitate the reporting of Non-Conformances. Businesses can enhance their reputation and showcase their dedication to excellence by adhering to these requirements.
The smooth running of any organization requires effective communication. The use of Non-Conformance Reports can enhance communication by ensuring that all pertinent parties are informed about issues and their solutions.
Enhancing communication and coordination among departments can prevent redundant efforts and the squandering of resources. Issues related to requirements that arise in one department can be effectively communicated to other departments for their consideration during the development process.
Reporting on non-conformances across various aspects of the organization, such as time, people, tools, operations, and safety, enables you to monitor their effects on the overall business.
The Non-Conformance board will address any issues that may arise and have a significant impact on the quality of construction. By doing so, they ensure that the maximum return on investment is achieved.
We can help you to manage your project for better business revenue.
Experience seamless project management with our free plan!