Daily Progress Report (DPR) in construction
The results of the planning and design process of a project are the Daily Progress Reports (DPRs). With the help of Livefield app, it is easy to make a DPR report.
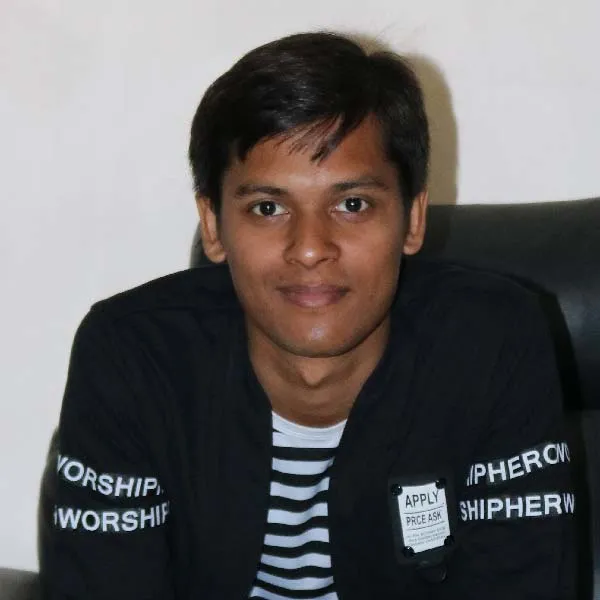
Hey guys! Construction is such an exciting adventure, filled with both challenges and chances to shine! When it comes to construction projects, it's crucial to identify opportunities and risks and manage them like a pro! If a risk isn't handled properly, it can totally ruin a construction project. For proper project management, we need to identify, control and monitor risks properly.
Uncertainties that pose a risk are not always negative. Effective risk management can result in higher profits, positive client relationships, and the opportunity for future projects. The construction industry poses a greater challenge for risk management compared to other sectors. In manufacturing projects, the primary risks are typically related to labor and supply chain disruptions. However, in the construction industry, risks are more varied and can be difficult to predict.
A hazard refers to a situation that can potentially endanger life, the environment, property, or personal safety. A hazard on a construction site refers to any problem that poses a threat to the safety and physical well-being of individuals present at the site. Hazards are situations that have the potential to escalate into incidents or disasters.
Uncertainty refers to the probability of an event taking place when there is insufficient or incomplete information available. Uncertainty refers to a situation where there are multiple possible outcomes that are likely to occur.
Conversely, a risk is the result of an event that is anticipated based on statistical probability. The likelihood of failure is high when there are risks involved. A risk is any event with a high probability of impeding the progress, quality, and cost of the project. Hazards and uncertainties are situations that require caution, but they are not necessarily classified as risks.
As previously mentioned, the construction industry is a volatile business that involves a significant amount of risk. Many of these risks are repeat offenders, as we will discuss. Here are some of the common hazards that may arise during the construction phase.
Without a doubt, delays are the most prevalent risks in construction. Although contracts typically include timelines and schedules, they often fail to account for all variables. As a result, this causes delays that impact nearly everyone involved. Delays in a project can occur due to various reasons such as inadequate project management, change orders, accidents, or incorrect scheduling.
Preparing for delays beforehand is the most effective way to prevent them. To minimize the cumulative effect of delays on a project, it is important to ensure that communication is always open among the project's stakeholders.
Construction projects are known for generating a large amount of paperwork. The tasks involved can vary, including change orders, appraisals, licenses, and approvals. Some contractors have poor document management practices and may store their paperwork on the dashboard of their pickup trucks. Losing a single receipt or piece of paper can result in both time and financial costs. The level of risk varies across different occupations. Managing paperwork for large projects that involve multiple subcontractors with different submission processes and compliance requirements can be a challenging task. Improper documentation related to licensing and insurance can result in legal problems.
Being organized is the best way to avoid such situations. It is important for every contractor to have a document checklist that they can use to verify that all necessary paperwork is in order.
Pricing of materials and profitability are among the most crucial risks to consider in a contract. If a contractor enters into a lump sum contract without leaving enough room for emerging costs, they may be vulnerable to fluctuating material prices. Factors that could potentially increase costs include natural disasters, a surge in demand for materials within a particular region, or labor-related problems.
Contractors can account for sudden increases in prices by adjusting the mark-up to accommodate the rise in costs.
The construction industry frequently faces the challenge of locating skilled labor. Many contractors do not maintain a full-time staff and instead hire workers on a project-by-project basis, depending on the scope and complexity of each job. Insufficient workforce on a project can cause delays for all parties involved if a contractor is unable to complete the project due to a lack of manpower. Delaying the timeline has a negative impact on the profitability of a project. If a union is present, the unity among workers can lead to a complete walkout during a strike.
To address labor shortages, a contractor can establish community partnerships and offer employees a competitive wage package.
Experienced subcontractors often encounter difficulties when collaborating with a new contractor. They are unaware of his work experience and organizational skills. A contractor who lacks organization can jeopardize the success of the project.
Miscommunication and conflicts can arise due to improper project management. The aforementioned issue can result in a chain reaction of negative consequences for other projects that a contractor is overseeing, as well as scheduling conflicts. Contractors should establish effective systems to ensure that their projects run smoothly and according to plan.
Poorly defined scope of work is a management issue that can negatively impact a project's success. Maintaining focus on a project can be challenging when the scope is not clearly defined.
Entering into cost-plus contracts is one of the best ways to deal with an unclear scope of work. Entering into a lump sum contract can be risky when the scope of work is unclear or ambiguous. The lack of clarity in the scope of work is likely to negatively impact profitability. The reason for this is the rise in material costs, site conditions, and other variables that affect the project.
Improving communication with project stakeholders at all levels is another effective approach to enhancing profitability. This will assist you in maintaining profitability.
Change orders are modifications to the original scope of work agreed upon in a contract.
Change orders are an inevitable aspect of the construction industry. Inadequate management of change orders can impede the success of a project, resulting in missed opportunities and exceeding the budget.
It is crucial to document and sign any change orders that arise. If the work done by a contractor is not properly documented, they may end up doing tasks that the client did not approve of. Payment disputes are inevitable as a result of this.
To effectively manage change orders, it is important to maintain all the required documentation and promptly submit any changes to prevent payment disagreements.
The payment process in the construction industry is often lengthy. Contractors are affected by these disputes as they result in a delay in receiving their paychecks. Loans and high interest rates can significantly impact the profit margins of a construction company, and in some cases, even cripple their operations. Over time, a contractor may find themselves in a situation where they are barely breaking even on a project, but still relying on the cash flow to fund other projects. Issuing payment notices on time can help contractors avoid payment disputes. A well-written contract should include a clearly defined payment schedule. Additionally, any violation of the terms outlined in the contract will be considered a breach of contract.
Construction sites are dynamic environments where conditions can change rapidly, potentially creating unprecedented health and safety hazards. Severe fatalities can result from major accidents. The objective is to guarantee that the project is executed without any accidents or incidents, starting from the beginning until its completion.
Accidents not only pose a risk to the safety of workers but also result in decreased productivity for the project. The reason for this is the workers' low morale in the project. Low productivity can result in project delays and budget overruns.
Training the staff on how to prevent accidents and handle them effectively when they occur is the most effective approach to mitigating health and safety risks. Before the project kickoff, it is crucial to inform all staff and subcontractors about their safety obligations.
The rate of financial failure in construction projects is significantly high and concerning. Filing for bankruptcy is often seen as the most convenient solution for companies facing economic difficulties. Following bankruptcy, certain companies undergo restructuring and emerge as stronger entities, while others fail to recover and ultimately go out of business. If bankruptcy occurs, all progress on a project is frozen. Filing for bankruptcy can result in the seizure of on-site equipment or previously financed materials. Although rare, bankruptcy is a potential risk that can arise during construction projects.
Despite its name, structural risk is not related to the actual physical structure of a building. Structural risk pertains to the financial framework of an investment and the corresponding entitlements that it offers to its individual participants.
It is crucial to have structures in place when constructing. Having insurance not only helps you avoid unexpected expenses, but it also ensures that the process runs smoothly. The financial structure of the project poses a significant risk. Maintaining accurate expenditure records throughout the construction process is essential to avoid the risk of overspending and underquoting. Furthermore, maintaining accurate financial records ensures that all material purchases are properly accounted for. If a warranty needs to be redeemed due to a breakage, there is a reference point available. There exists a comprehensive record of market prices that can be used to track inflation and purchasing rates.
Contractors in modern construction projects often encounter the risk of employing unskilled labor, which can result in reduced productivity. Unskilled workers may pose a risk of project delay and require closer supervision. Managing an unstructured labor force can be challenging, and it is important for a skilled project manager to oversee matters such as safety and skills training for the team.
For any contractor, it is crucial to prioritize obtaining the appropriate materials when undertaking construction. Choosing the wrong materials can have dire consequences that are often irreparable. Choosing materials requires careful consideration, as the use of counterfeit materials poses a significant risk. Poor construction practices may result in structural collapse or accidents during or after construction, which could lead to liability.
Since we have already covered the common construction risks, it is important to identify any risks that are specific to the project at hand. It is advisable to identify risks at the earliest possible stage of a project. During the preconstruction stage, the project team primarily identifies project risks. If risks are not identified and managed in a timely manner, it essentially means that the risks associated with a project are being accepted.
Conducting brainstorming sessions with project stakeholders is the most effective approach to identify risks. The objective is to identify various potential scenarios and their impact on the project, rather than solving any specific problem. During the brainstorming process, the project team reviews similar projects, taking into account their scope, location, risks involved, and the measures taken to mitigate those risks.
Furthermore, it is recommended that the project team conducts frequent meetings throughout the entirety of the construction process. Conducting these meetings addresses any current or potential issues that may arise in the near future.
In some cases, when a risk becomes a reality, it has the potential to negatively impact a project. At times, a project can fail due to a series of minor risks that accumulate over time. In order to achieve a healthy growth equity curve, a company should prioritize investing in risk management. What are the most effective methods for mitigating construction risks? Establishing effective processes is the optimal approach to facilitate the smooth and efficient execution of sound decision-making. Here are the steps you should follow to effectively manage construction risks.
It is easier to prevent an accident than to handle one. The initial step to prevent risks is to identify and list all potential sources of risks. Risks are categorized into different types such as occupational, financial, contractual, project-related, natural, or stakeholder risks. The identified risks are prioritized based on their likelihood of happening, and preventive measures are implemented to mitigate them. In certain situations, declining a project or re-evaluating a contract may be necessary to steer clear of potential risks. It is wise to avoid ventures with unfavourable risk-reward ratios altogether.
At times, it may not be feasible for your company to assume a risk associated with a project. Insurance policies are a means of transferring risk. It's important to keep in mind that insurance policies don't cover all possible risks. To ensure you have the appropriate coverage, it's recommended that you have a discussion with your insurance provider about the specific liabilities they are willing to cover. Another approach involves establishing contractual agreements between the general contractor and subcontractors or suppliers, whereby they agree to assume partial risks associated with a project. The optimal approach would be to engage in a discussion with the project stakeholders and come to a consensus regarding the risks that each party will assume. The client and general contractor must come to a mutual agreement regarding the allocation of risks that each party is willing to assume
In case the project team is unable to eliminate the risk, they should implement measures to minimize it. The likelihood of unwanted incidents can be significantly reduced by ensuring that workers receive appropriate training and wear the necessary safety equipment. It is advisable for the team to break down risks into specific actionable items. Additionally, the contractor should avoid overcommitting resources when dealing with multiple risks.
At times, we may recognize potential risks but choose not to accept them. We should not make the decision to accept risk lightly. The individual who is responsible for assuming a risk should evaluate the potential consequences of taking on that risk. Accepting low impact risks may seem easy, but it's important to carefully manage high probability and high impact risks. If not managed properly, these risks could have a detrimental effect on the project and the party responsible for bearing the burden.
Having a team equipped with the appropriate skillset distinguishes your project from others. The key to avoiding risks and delays in a project is to have the right people who can anticipate and counter any challenges that may arise. This approach is more effective than not knowing what to do and exposing the project to various risks.
The law provides clear guidelines on how to handle the consequences of risk. Keeping a detailed log of the rules that were followed and the compliances that were made may prevent problems from escalating throughout a building project.
This is used for procuring goods and services for construction projects. It shifts some of the blame away from you and onto the other person. When a claim is made that an on-site process was followed but the product utilized was not in the correct condition or make as per its manufacturing address, any resulting risk may be mitigated. Warranties here are useful and mitigate the danger.
Before beginning the project, it is important to test and assess the technology being used. You can save a lot of time, money, and effort by avoiding this step. Reviewing items provides an insight into what to anticipate, and what to avoid, during a construction project, when the effect of risk might be too great.
We can help you to manage your project for better business revenue.
Experience seamless project management with our free plan!