Daily Progress Report (DPR) in construction
The results of the planning and design process of a project are the Daily Progress Reports (DPRs). With the help of Livefield app, it is easy to make a DPR report.
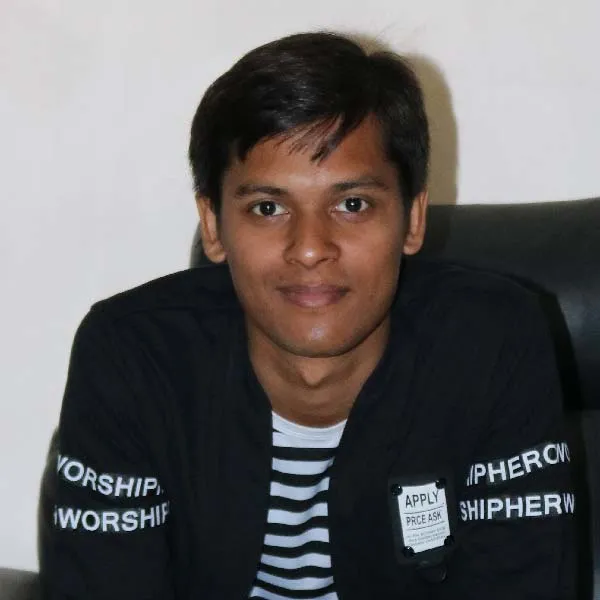
Industry-wide cost management and resource planning are critical now more than ever. This warning couldn'tpos;t have come at a better time for the construction industry. During the last five years, KPMG found that more than two-thirds of construction projects overestimated their costs by more than 10%.
Despite the fact that efficient job costing and cost management is a fundamental requirement for construction projects, Construction managers struggle to maintain projects under budget owing to continually changing project needs, a dynamic business environment, and inefficient data collection methods.
As per KPMG’s Global Construction Survey – 2016, Just 31% of all projects came within 10% of the budget in the past three years.
There are a lot of moving factors when it comes to controlling a construction project's budget. Contractors, subcontractors, customers, site workers, and office employees must collaborate to collect and exchange data so that executives can plan and take financial decisions with the knowledge they have. In the past, the construction industry has been notorious for being split up, which led to higher costs and inadequate budget control.
However, as industry use of technology accelerates, project managers may leverage integrated software solutions to alter inefficient processes, enhance communication, and boost productivity.
Here are five ways that technology may assist construction companies in properly managing project costs.
The financial and budgetary requirements of each construction project are unique. Budgeting for certain projects might be wildly speculative and even outright wrong. If that's the case, when construction starts, project managers may find they need to use alternative materials or, approach the project in a different way. Construction manager have a tough time estimating a project's total costs due to this uncertainty.
Traditional design-bid-build models may be replaced with more efficient designs build by using BIM simulation technology. As more organizations employ BIM technology to simulate projects before on-site work starts, Project managers may utilize modelling software to assess supply and financial demands of different construction techniques, so they may choose the most cost-effective mode of construction.
Construction projects are quite dynamic in nature. During the course of a project, clients often revise their requirements or the scope of the work.
The rework accounts for almost 30% of all work completed by construction companies. As information is given to them, they must change their budgets, design new procedures, and convey these changes to the rest of the team in real time.
A number of communication platforms and techniques are used in the construction business, making it difficult to communicate these changes between the office and construction site. Businesses may utilize project management software to communicate more quickly with the most recent information on project requirements and changes in policy. In this way, construction projects are able to stay flexible and swiftly adapt to project changes, while reducing the amount of rework required.
The main lesson the epidemic has taught companies is that even the most well-planned project plan may be thrown off course by unanticipated market circumstances. Inflation, changing labor costs, and fluctuating supplier prices are particularly problematic for construction projects. Construction is no exception. These considerations are often mentioned during resource planning in the early stages of a contract, although they are generally static (not dynamic). As a result, there's a good chance that project managers who rely on early budgeting data are using obsolete market data.
Project managers typically have to juggle a variety of tasks while on-site, which makes it tough to remain on top of changing market conditions. To address this knowledge gap, AI-based software can notify project manager when rules or expenses suddenly change. In addition, software aids in the identification of inefficiencies in a project.
On a daily basis, construction sites produce enormous amounts of data. Managers may use this information to see how the work is going on site and how it compares to the original project plans. But because of inefficient data collection on construction sites, a large percentage of this information is either ignored or squandered.
Having access to real-time data collected and delivered on-site allows project managers to swiftly identify and address productivity blockages, resource shortages, and staffing issues. Livefield, for example, is a digital system that can collect, organize, and analyze real-time project data. In this manner, decision makers can detect costly inefficiencies (and avoid them) as they arise.
Businesses in the construction sector are increasingly looking for innovative methods to boost productivity and efficiency on the job site as demand rises and the workforce shrinks. Doing so reduces turnaround time and operating costs for construction firms. 76% of construction businesses have invested in connected technology like drones and robots in an effort to reduce costs and improve margins.
The use of specialized digital technologies may help construction project managers save costs in all areas. It's important to keep in mind that the benefits of BIM, automation, robots, and other tools go well beyond the specific fields in which they are used. Business leaders may save money by selecting the solutions they need to get the most value out of their technology stack.
We can help you to manage your project for better business revenue.
Experience seamless project management with our free plan!