Daily Progress Report (DPR) in construction
The results of the planning and design process of a project are the Daily Progress Reports (DPRs). With the help of Livefield app, it is easy to make a DPR report.
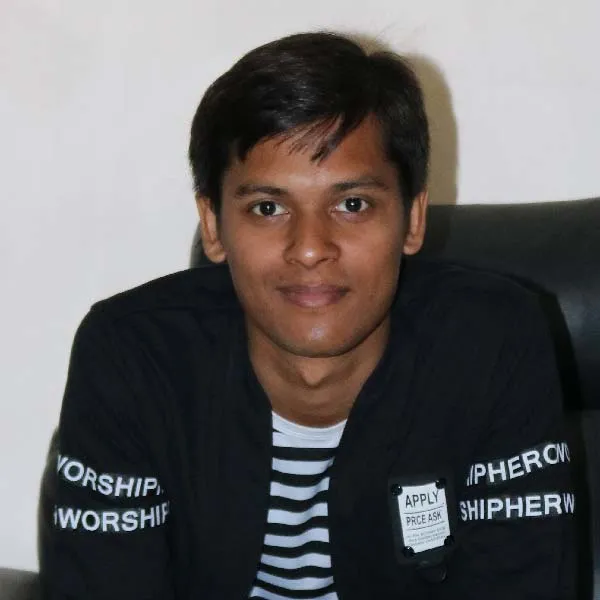
Cement, a crucial component of every construction project, is a binding agent that, after it dries, firmly attaches to building elements like stones, bricks, tiles, and so on. Limestone (calcium), sand or clay (silicon), bauxite (aluminum), and iron ore are the primary components of cement, while other materials such as shells, chalk, marl, shale, clay, blast furnace slag, and slate may also be used. Cement facilities take the raw materials and treat them with heat to create a rock-hard product, which is then pulverized into a powder and packaged for sale. When cement is combined with water, a chemical process takes place, creating a paste that, as it sets and hardens, binds together the various components of a building.
Cement plays a crucial role in the development of cities. It's a key ingredient in both mortar and concrete, and both help keep the pieces of our infrastructure together and safe. Cement, water, sand, and gravel are the four main components of concrete, whereas cement, water lime aggregate make up mortar. Both of these are used in the construction industry to bind building materials together, fill or seal gaps, and create aesthetic designs. When cement is combined with water-repellent materials like silicates and aluminates, the resulting hardened mass may be utilized to prevent water seepage.
To figure out how much cement one would need when mixing mortar or concrete, or even cement and water only, use this calculator.
The vast majority of cement used nowadays is ordinary Portland cement (OPC). Based on the cement's strength at 28 days, the OPC was categorized into three grades in India: 33 grade, 43 grade, and 53 grade. We refer to cement as "33 grade" if its compressive strength after 28 days is at least 33 N/mm2, as "43 grade" if it's at least 43 N/mm2, and as "53 grade" if it's at least 53 N/mm2. The actual manufacturing strength of these cements, however, exceeds the BIS requirements.
As blended cement becomes more widely used because to its lower energy consumption, reduced environmental impact, cheaper cost, and other technological advantages, OPC production decreases over the globe.
This cement is very much like regular Portland cement. Because of how quickly it gains strength, it is also referred to as high early strength cement. One should not mistake rapid hardening cement, which gains strength at a faster pace, with quick-setting cement, which just hardens rapidly. At three days of age, rapid hardening cement reaches the same strength as regular Portland cement does after seven days.
Rapid hardening cement, as a result, emits much more heat of hydration in the early stages. Therefore, mass concrete building should not use quick hardening cement. It is suggested that rapid hardening cement be used while doing the following:
Extra rapid hardening cement is obtained by intergrinding calcium chloride with rapid hardening Portland cement. The normal addition of calcium chloride should not exceed 2% by weight of the rapid hardening cement. It is necessary that the concrete made by using extra rapid hardening cement should be transported, placed and compacted and finished within about 20 minutes. It is also necessary that this cement should not be stored for more than a month.
Extra rapid hardening cement accelerates the setting and hardening process. A large quantity of heat is evolved in a very short time after placing. The acceleration of setting, hardening and evolution of this large quantity of heat in the early period of hydration makes the cement very suitable for concreting in cold weather,
The strength of extra rapid hardening cement is about 25% higher than that of rapid hardening cement at one or two days and 10–20% higher at 7 days.
Did you know?
Use of Extra Hardening Cement in prestress concrete construction is prohibited.
The use of sulphate resisting cement is recommended under the following conditions:
As its name implies, this cement sets quickly. Reducing the gypsum concentration during clinker grinding brings out the early setting feature. This cement must be mixed, poured, and compacted as soon as possible. Its primary use is in underwater construction that requires the use of pumps. In these situations, quick-setting cement may cut down on pumping costs and save time. Some common grouting tasks may also benefit from the use of quick-setting cement.
Super sulphated cement is manufactured by grinding together a mixture of 80-85% granulated slag, 10-15% hard burnt gypsum, and about 5% Portland cement clinker. The super-sulphated cement is extensively used in Belgium, where it is known as “ciment metallurgique sursulfate.” In France, it is known as “ciment sursulfate”.
It is well known that hydration of cement is an exothermic action which produces large quantity of heat during hydration. Formation of cracks in large body of concrete due to heat of hydration. So, Low heat cement produces less heat or the same amount of heat, at a low rate during the hydration process. A low-heat evolution is achieved by reducing the contents of C3S and C3A which are the compounds evolving the maximum heat of hydration and increasing C2S. It is used in mass concrete construction, such as dams, where temperature rise by the heat of hydration can become excessively large.
Portland pozzolana cement can be used in all situations where OPC is used except where high early strength is of special requirement. As PPC needs enough moisture for sustained pozzolanic activity, a little longer curing is desirable. Use of PPC would be particularly suitable for the following situations:
Air-entraining cement is made by mixing a small amount of an air-entraining agent with ordinary Portland cement clinker at the time of grinding. Air-entraining cement will produce at the time of mixing, tough, tiny, discrete non-coalesceing air bubbles in the body of the concrete which will modify the properties of plastic concrete with respect to workability, segregation and bleeding.
For manufacturing various coloured cements either white cement or grey Portland cement is used as a base. The use of white cement as a base is costly. With the use of grey cement only red or brown cement can be produced. Coloured cement consists of Portland cement with 5-10% of pigment.
Hydrophobic cement is obtained by grinding ordinary Portland cement clinker with water repellant film-forming substance such as oleic acid, and stearic acid. The water-repellant film formed around each grain of cement, reduces the rate of deterioration of the cement during long storage, transport, or under unfavourable conditions. The film is broken out when the cement and aggregate are mixed together at the mixer exposing the cement particles for normal hydration. The film forming water-repellant material will entrain certain amount of air in the body of the concrete which incidentally will improve the workability of concrete.
Ordinary cement mortar, though good when compared to lime mortar with respect to strength and setting properties, is inferior to lime mortar with respect to workability, water retentivity, shrinkage property and extensibility.
Masonry cement is a type of cement which is particularly made with such combination of materials, which when used for making mortar, incorporates all the good properties of lime mortar and discards all the not so ideal properties of cement mortar. This kind of cement is mostly used for masonry construction.
Concrete made with ordinary Portland cement shrinks while setting due to loss of free water. Concrete also shrinks continuously for long time. This is known as drying shrinkage. Cement used for grouting anchor bolts or grouting machine foundations or the cement used in grouting the prestress concrete ducts, if shrinks, the purpose for which the grout is used will be to some extent defeated. A cement which suffers no overall change in volume on drying is known as expansive cement.
High alumina cement is obtained by fusing or sintering a mixture, in suitable proportions, of alumina and calcareous materials and grinding the resultant product to a fine powder.
Recommended Value for dry / wet volume ratio
- 1.54 for concrete
- 1.33 for mortar
V Cement = 16.94 xTo find Volume of each component
V component = Dry Volume xParts from TotalTotal number of parts
The process of calculating the amount of cement required in a mortar mix is similar to the aforementioned procedure. The sole disparity lies in the absence of gravel within the mixture.
Experience seamless project management with our free plan!
We can help you to manage your project for better business revenue.