Daily Progress Report (DPR) in construction
The results of the planning and design process of a project are the Daily Progress Reports (DPRs). With the help of Livefield app, it is easy to make a DPR report.
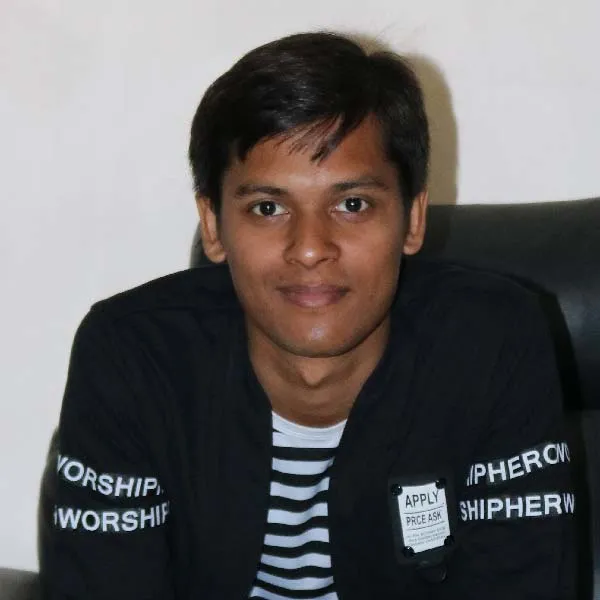
Concrete is quickly replacing asphalt, bitumen, and other paving options as the material of choice for new driveways. Concrete driveways, often known as cement driveways, are distinct from other road building techniques due to the wide range of decorative alternatives available.
The contractor in charge of laying the concrete for the driveway must ensure that the process goes smoothly if the driveway is to meet the necessary standards for quality, appearance, and durability. The functionality and visual appeal of a concrete driveway are entirely dependent on the quality of the construction and the materials utilized. The following requirements must be met when constructing a concrete driveway.
Preparing the subgrade is essential for achieving consistency in soil type and compaction. Meeting this standard helps ensure the driveway can handle the weight of vehicles and other vehicles using it.
This aids in obtaining:
If weak soil is discovered during preparation, it should be replaced with a stronger material like crushed rock or gravels. A geotechnical engineer must be consulted to determine the site'spos;s soil qualities. Compaction may be accomplished using either rammers or vibratory compactors.
Ready-mix concrete is recommended by ASTM C-94 for use in the construction of concrete driveways due to the consistency it offers. Using the right concrete mix may prevent issues of random cracking. Among the requirements are:
Plain concrete is often used for driveways that aren'tpos;t heavily used. Concrete or reinforced concrete might be used to strengthen the driveway'spos;s foundation. In high-traffic areas, including driveways, reinforced concrete is your best option. No amount of reinforcing can stop fractures from developing. However, if fractures do appear, the rebars will keep them together and stop them from spreading. Reinforcement for a concrete driveway might take the shape of either a wire mesh or a grid. By placing blocks beneath the rebars, the reinforcement may be positioned accurately in the middle of the concrete driveway. Synthetic fibers are increasingly being used as reinforcement due of their effectiveness in preventing shrinkage cracks. They are employed in conjunction with primary steel reinforcement, but not as the primary reinforcement itself.
The thickness used has a significant impact on the driveway's structural capability. A concrete driveway should be at least 4 inches thick. Based on driveway requirmeents and standards, an increase from 4 to 5 inches improves structural capacity by 50%.
Because of the concentrated stress at the margins, The concrete curbs around the driveway are thickened by an extra 1-2 inches.
Overworking the surface or performing operations over bleeding water on the surface are the two most common causes of mistakes in the finishing process of a concrete driveway. The following procedures are used to complete the finishing of concrete driveways.
The problems of random cracking may be mitigated by the use of control joints at suitable intervals. Driveways made of 4 inches of concrete often have 10 feet separations between each slab. Cracking at random does not indicate serious structural collapse. On the other hand, it diminishes the attractiveness of the driveway.
Avoiding triangular or rectangular areas in your joint layouts might help keep your joints from cracking at random. Control joints should be one-fourth of the thickness of the driveway. Isolated joints must be provided at all points where the driveway connects the sidewalk, other pavements, or garage floor slabs. Joints should be planned out in advance of constructing a driveway.
Concrete driveways benefit from a well-thought-out drainage system that keeps water moving. Concrete driveway drainage may be achieved in two ways,
When laying a concrete driveway, most contractors skip the curing phase. Curing is just as crucial as the other processes described. Curing the surface promptly after completing is essential. Curing can be done by:
The typical suggested cure time for a concrete driveway is 7 days. If the curing process isn't done properly, the strength could be dropped by 50%.
Experience seamless project management with our free plan!
We can help you to manage your project for better business revenue.